Development of the safety culture
The corporate safety culture forms a core component of OHS management. In 2018 corporate initiatives focused on improving the corporate safety behaviour of employees and contractors, building a comprehensive training system, further developing the occupational safety risk assessment methodology, and organising events to improve the corporate safety culture, for example EVRAZ Safety Week.
Occupational health and safety trainings
OHS education and trainings are aimed at providing employees with the knowledge and skills that they need to perform their work safely. Each EVRAZ business segment has its own training centre. EVRAZ is legally required to provide health and safety training for employees twice a year, which includes one week of training and an exam. All staff complete tests that comprise questions on working instructions and HSE regulations. Engineering and technical specialists are certified by commissions on their knowledge of safety rules, emergency responses, and annually on HSE as a whole. In addition, employees must a complete test on emergency procedures after extended periods of leave.
In addition to legislative requirements, EVRAZ places great emphasis on practical exercises. Both employees and contractors of all levels undergo training courses and practical tests on various simulators. Coal segment continues to develop “Virtual mine” project, which includes simulators on electrical safety, working at height and others. The Siberia region of Steel segment actively exploits its training centre and plans to expand training facilities next year. In total EVRAZ provides almost 2.5The figure comprises data on EVRAZ ZSMK (incl. Evrazruda), EVRAZ NTMK, EVRAZ KGOK, Raspadskaya Coal Company. million man-hours on OHS education and training of employees.
Leadership programme for managers
With a view to further enhancing corporate safety behaviour, EVRAZ needs to further improve the level of engagement from managers. Line managers, as part of the overall leadership team, play an essential role in developing the health and safety culture. In 2018 we launched a leadership programme for line managers, which forms part of a larger programme to build commitment to health and safety issues among all EVRAZ employees and to foster safe practices at operations. The leadership programme includes criteria for determining safe behaviour from managers, evaluating actions, and HSE-related feedback sessions.

In order to foster a culture of safety at EVRAZ we hold annually the EVRAZ Safety Week. In 2018 the fifth event was held, from 16 to 22 of April, and encompassed various health and safety activities. Employees have an opportunity to get tested for HIV, participate in a quiz on safety practices and procedures, and take part in a campaign where cigarettes are exchanged for health drinks (in canteens at EVRAZ NTMK and Kachkanarsky GOK volunteers collected more than 2,000 cigarettes).
The Safety Week provides an opportunity to discuss important topics, not only with our employees, but also with citizens. This year’s focus was on holding special lessons on transport and fire safety for schoolchildren and students.
EVRAZ updated the effectiveness evaluation system for managers, which now includes metrics on HSE engagement. In 2018, 41 subdivisions of the Siberia region of Steel segment conducted evaluations of managers; a further 50 subdivisions will conduct evaluations in 2019.
In addition to developing leadership programmes for line managers, EVRAZ is keen to involve employees of all levels in developing the safety culture.
Behaviour safety conversations and safe work procedures
Behaviour safety conversations and safe work procedures make up another part of the EVRAZ safety culture programme, and aim to raise awareness and engagement among employees. These instruments help record unsafe behaviour and remedy it before any incident occurs. In previous years our focus was on developing a practice of behaviour safety conversations and creating internal IT solutions that record the number of these conversations and track trends and remedial actions. In 2018 we mainly focused not on the number of conversations and observations performed by managers, but on their quality.
In addition to a previously developed quantitative assessment indicator, a qualitative indicator was introduced. Each behaviour safety conversation and observation held by a manager is evaluated on a three-point scale system. A manager receives one point for recording a violation of safety rules; for example, the incorrect use of personal protective equipment. Two points are given to a manager in the event of a recorded change in behaviour from an employee after a safety conversation. Lastly, three points are given if there is an improvement to a previously developed safe work procedure or other aspect of corporate safety. As well as the three-point scale system, a unified format of safety conversations was introduced. A successful pilot project was launched at EVRAZ ZSMK. There are plans to introduce changes at all Group enterprises in 2019.
Identifying and testing key health and safety risks
The identification of key health and safety risks forms an integral part of the EVRAZ OHS system. The Health and Safety Directorate performs risk assessments and the further development of initiatives with quantitative and qualitative targets. Six main risks account for 70–80% of serious injuries and fatalities at EVRAZ. The top three are rock falls, falling objects, and moving machinery. The identification of health and safety risks was a priority topic at the HSE Strategy Session in 2018.
During the HSE Strategy Session it was also decided to update safety tests for employees. Instead of testing how familiar employees are with health and safety regulations, the Group will now focus on testing adherence to regulations, by introducing a case study approach to testing. The topic of risk identification has been incorporated within case studies and employees are also given practical tests.
In order to mitigate against safety risks related to the human factor, psychophysiological tests were developed to assess personal risk tolerance. In 2018, in the Siberia region of Steel segment, the psychophysiological testing of electricians and blasting professionals was performed. In 2019 it is planned to test metalworkers and machine operators. In the next reporting period psychophysiological testing is also planned for the Urals region of Steel segment.
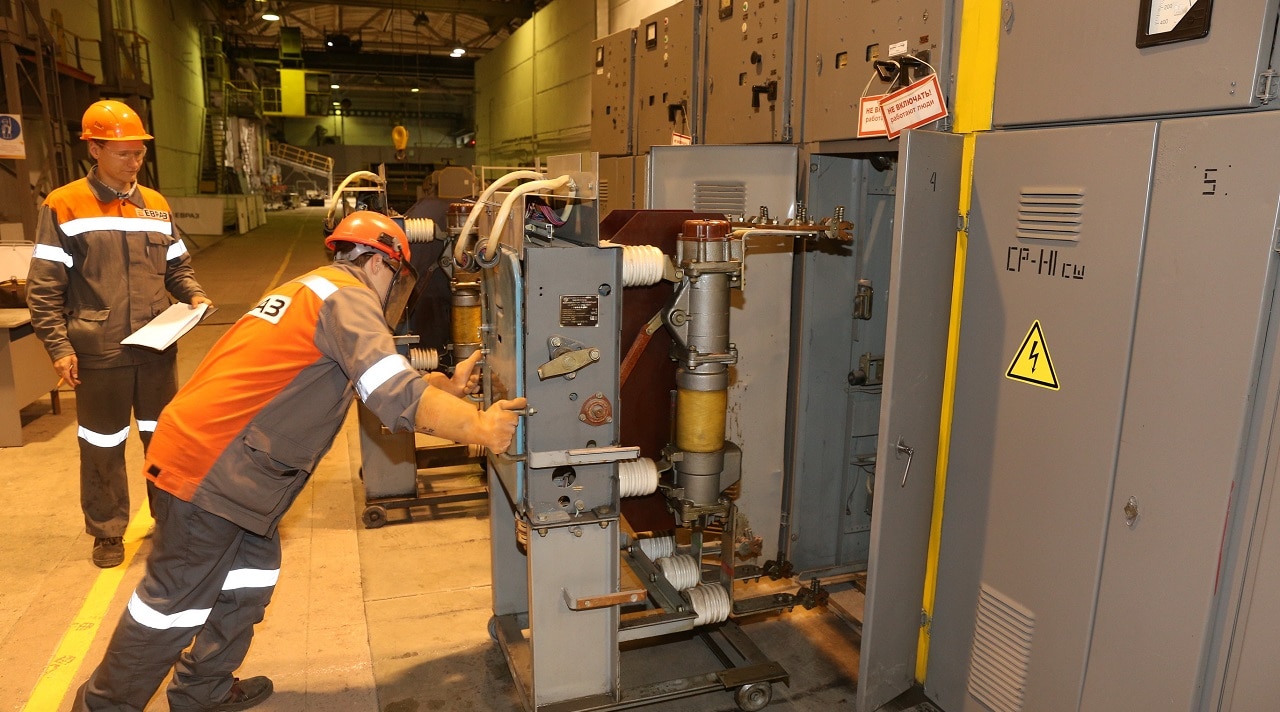